Solution 自動車製造のためのアーク溶接ソリューション
ASSYの生産性を上げる
製品組み立て品質確保に実機の試作を繰り返されていませんか?
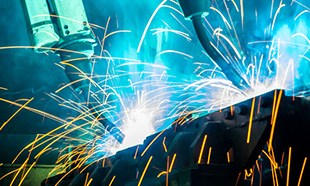
車両製造では抵抗スポット溶接が主流の接合方法と思われがちですが、厚板や複雑な形状への許容度が高いこと、線接合により接合領域が大きいことにより接合強度、製品剛性が得られることから、アーク溶接の適用範囲は非常に広いのが実情です。
上記のような特徴を持つため、足回り部品やトラックやSUVのような大型車のフレームなどに用いられますが、ハイテン化が進み、その鋼材成分による圧接手法の限界や薄板化に対し剛性を確保する目的で、その施工条件の不利を克服した手法を取り入れながら、ボディ骨格部品への適用も考えられてきています。
加えて、これらの対策はどれも現場担当者の経験に依存しているため効率化が難しく、技術継承も課題のひとつとなっています。
アーク溶接は、その手法の特徴上大きな熱が入力されるため、製品の変形が大きくなりがちです。そのため、接合後の組み立て寸法精度を確保するためには、試作を行って接合条件を決めていくことが多くなります。
しかし、試作は1回ごとにワークの作成や設備の設定、試験を行うため、要因の特定や対策案の有効性確認のための試作を繰り返せば、その回数が増えるたびにコストが増加します。その上、工程設計変更にもコストが発生します。また、工程設計を変更できない場合は修正方法が限定されたり、人の手による修正が必要になることもあります。
車両製造ではこのようなコストを削減するため、シミュレーションによる設計時の対策検討が進んでいます。
接合設計段階での不具合対策を徹底する
溶接の工程設計にシミュレーションを用いると、接合条件や治具を含めた施工条件の変更検討が容易に行えます。
接合順序や治具配置を変更した場合の影響が可視化され、手順を追って確認できるため、問題の要因特定も対策の確認も容易になります。その結果、試作に頼っていた不具合対策を設計段階で行えるようになり、試作の工数を減らすことができます。
こうして後工程に余裕が生まれれば、どうしても必要な試作や工期後半に入ってからの設計変更への対応などにも時間を割けるようにもなります。また、変形量の分布やアニメーションなど視覚的な結果を共有することで、溶接の現場とのコミュニケーションもとりやすくなります。
車両の製造は、高度なすり合わせ技術であると言えます。後工程で発生する不具合は、単一の工程に由来する場合もあれば、その前工程に由来する場合もあるかもしれません。また、逆に前工程の不具合を、次の工程で修正することが可能なのかもしれません。前後工程と連携したシミュレーションが可能になると、不具合の総合的な対策も考えられるようになります。
- アーク溶接へのCAE適用が進むメリット
-
- ・変更の選択肢が多い設計段階で溶接工程を検討できる
- ・変形低減できる設計が可能
- ・試作回数が減る
- ・設計後の不具合対策のための治具変更・追加がなくなる
- ・熟練者の対策技術を見える化できる
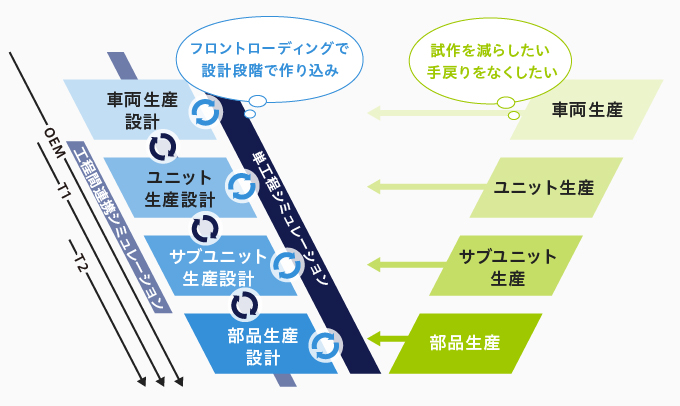
溶接シミュレーションの適用・機能向上が進んでいます
JSOLの溶接ソリューションでは、用途に応じて2つの手法を用意しています。溶接変形のみを短時間で計算する方法と、熱現象と応力などの構造現象を逐次解く方法です。
前者は、溶接個所が数十箇所を越えるような多数ある場合や、その順序検討など接合条件をいろいろ変更して検討する場合に適しています。多数の接合箇所の組み合わせを検討する場合、試作という方法には決定的な限界があります。シミュレーションは、今まで見えなかった要因や考えつかなかった対策を導き出す可能性を開きます。
後者は溶接の現象を詳細に再現します。溶接個所が1、2箇所程度と少なく、温度の影響範囲なども同時に確認したい場合に選択します。汎用構造解析ソフトウェアの標準であるAnsys LS-DYNAをすでにご利用の場合は、その溶接解析用入力データを作成するインターフェースとしてのオプションもあります。
いずれの方法においても、組み立て順序や治具の配置などを簡単に設定できるユーザーインターフェースを備え、解析のためのデータを作成する環境を整えています。その結果、溶接工程設計を事前にさまざまな条件で試すことができるようになりました。
こうした技術を活用することで、変形要因の根本対策や最適な溶接順序の探索、治具配置の効果やタクトタイムの確認も可能になりました。
変形要因の根本対策
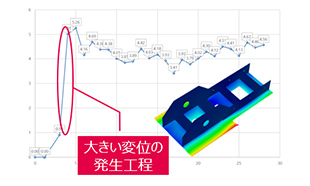
変形の大きい箇所が、どの溶接位置の影響により発生しているかを知ることができます。
溶接手順を順番に追いながら変形量がどのように変わっていくか見ることができるため、問題点の把握が早くなります。
試作を繰り返す工数や費用を削減できます。
最適な溶接順序を探索する
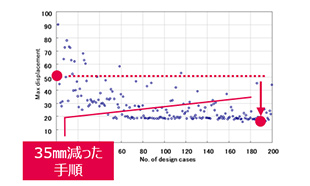
組付け製品の変形が一番小さくなる溶接順序を知ることができます。
溶接手順のあらゆる組み合わせを短時間で計算し、変形の小さくなる手順を自動で見つけ出します。
治具位置の設計
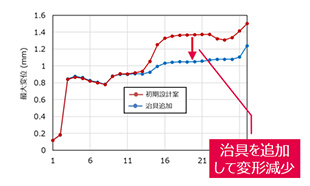
治具をどの位置に配置するか、製品の変形に対する治具の効果を知ることができます。
溶接手順を順番に追いながら,変形量がどのように変わっていくか見ることができるため,変形が大きくなる手順の近くに治具を配置することで、変形が抑えられることが確認できます。
タクトタイムも確認
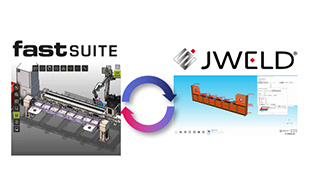
ロボットシミュレーターと連携して、溶接順序を変更した場合のタクトタイムを確認できます。
テックスイートジャパンのFastSuite※と連携して、溶接情報をやりとりすることで、解析で溶接順序を探索したあとのタクトタクトを確認できますし、解析の溶接順序設定も楽にできます。
- ※ fastSUITEは株式会社テックスイートジャパンが提供する汎用高機能ロボットシミュレーターソフトウェアです