
CAE Technical Library エンジニアレポート - CAE技術情報ライブラリ
12th European LS-DYNA Conference 2019 で JSOL が発表した講演の内容を紹介します。
今回とりあげるのは、DIFFCRASH を用いた数値モデルのバリデーションプロセス効率化です。
近年は製品開発サイクルの加速やコスト・環境意識の高まりを受け、製品開発において CAE が果たす役割はますます増えています。さらに自動車業界では CASE(Connected, Autonomous, Shared, Electrification)が今後重要になると考えられており、それらにリソースを割くためにも、現在行われている業務を効率的にこなすことが求められていきます。
有限要素を含む構造計算が業務効率化に役立つ場面として、
などが考えられますが、どちらも「鍵となる現象を正しく表現する数値モデルを用いること」が前提です。この前提を満たしているかどうかを確認するバリデーション作業をいかに早く終わらせるかが、開発効率に大きく影響します。そこで、試験結果と計算モデルの比較における実際的な課題と、モデルと試験方法の妥当性を効率よく検証する方法をご紹介します。
試験・シミュレーション結果の比較
下図は、クラッシュボックス落錘試験のシミュレーション結果(左)と実験結果(右)の比較です。
ムービーでは一見、現象が一致しているように見えますが、荷重カーブを見ると 4ms 付近からトレンドが大きく異なっていることが分かります。一般的に試験結果と計算結果は試験がすべて終わった後に比較されます。そのため、顕著な差が生まれた原因を動画から紐解こうとしても、不適当な画角や奥行きの計測困難などの要因で、差異発生の原因を動画から追及することは困難である場合が多いです。また、差異の原因に関する仮説を立てたとしても、実証するためには試験片の再調達が必要になることもあります。このように、試験結果と計算結果の差異を議論する材料の不足は、数値モデルのバリデーションに要する工数を増大させる要因のひとつになっています。
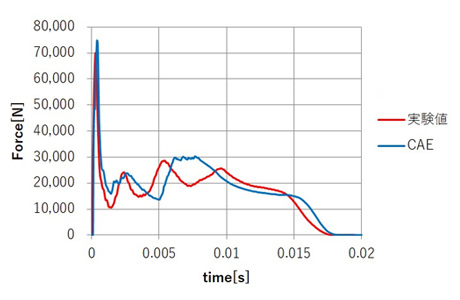
バラツキの再現
試験結果をシミュレーション結果と比較するにあたり、もう一点、注意すべき点があります。それは実験には必ずばらつきが含まれ、通常設計中央値を用いて行われるシミュレーションとまったく同じ条件である保証はどこにもないという点です。極端な例を挙げれば、上図カーブにおける差は大きいように見えますが、シミュレーションモデル側のパラメータを生産ばらつきレベルで調整することで実験結果が再現されるかもしれません。つまり、現実に起こるばらつきの再現度が不確定である以上「試験とシミュレーションからカーブ1本ずつを比較することにあまり意味はない」と言えます。
過去にばらつきを与え複数回計算した計算結果をモード空間上で可視化する手法をご紹介しました(DIFFCRASH を用いた 板成形におけるばらつき発生過程の可視化)。ここで、仮に、シミュレーション結果と同じように試験結果もプロットできるとします。そうすると、結果は下図にある2種類に分かれると考えられます。
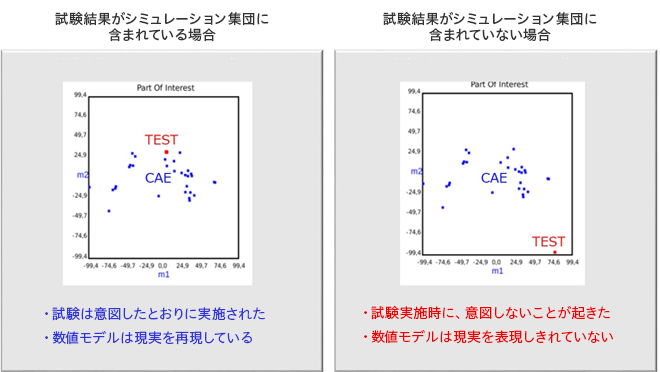
左図に示すように試験結果がシミュレーション集団に含まれている場合には、実験・シミュレーションともにうまくいっていると考えられ、「シミュレーションで起きると予測された変形が実験でも起きた」といえます。一方で、右図のように試験結果がシミュレーション集団に含まれていない場合は、試験・シミュレーションのどちらかまたは双方に問題があり「シミュレーションで起きると予測された変形が、実験では起きなかった」と言えます。開発効率向上のためには、後者の場合に試験とシミュレーションのどちらに(または双方に)どのような問題があるかを素早く効率的に理解することが重要です。
レーザースキャン結果に基づく変形モード比較
DIFFCRASH では新しく、試験から得られたレーザースキャン結果をシミュレーションにおけるモード空間に投影することが出来るようになりました。これにより以下のプロセスが可能になります。
- ・試験を忠実に再現したシミュレーションモデルを構築し、製品ばらつきを考慮したモンテカルロ計算を試験前に実施
- ・試験が終わった後すぐに実機のレーザースキャンを実施
- ・DIFFCRASH を用いて変形モードを比較し、問題があれば試験方法を含め調査
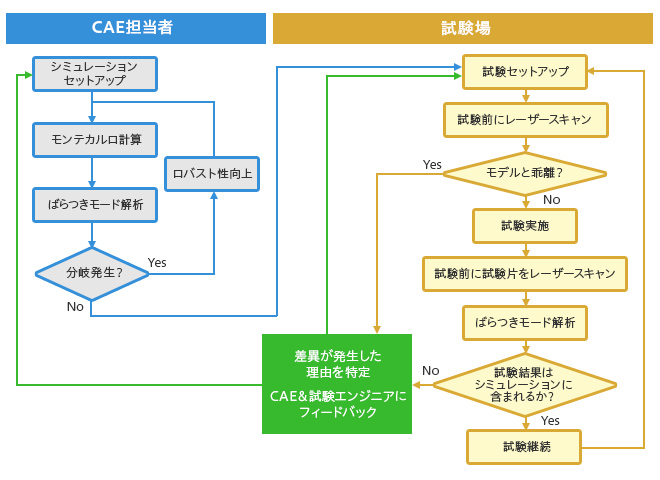
「鍵となる現象を正しく表現する数値モデル」は構造計算を用いての既存業務効率化に必須ですが、数値モデルのバリデーションにコストをかけ過ぎては意味がありません。何事も「想定外」に対処するにはコストがかさむため、初動が重要になります。今回ご紹介したように、DIFFCRASH によるばらつきを考慮した計算を活用することで、想定外の試験結果に対してもモデルの妥当性確認と結果差異原因の特定を速やかに進めることが可能になります。
今回ご紹介したプロセスで、試験結果や、製造工程が持つ個性をモデルに素早くフィードバックすることは、プロダクトライフサイクル上流である開発・設計におけるデジタルツイン実現に対する第一歩ではないでしょうか。
次回のエンジニアレポートでは、今回ご紹介した数値モデルのバリデーションの具体例をご紹介します。
DIFFCRASH についてご質問がございましたら、 こちら からお問い合わせください。